The Manufacturing Process of Your Transfers
Our manufacturing process is an amalgamation of advanced technology, high-quality materials, and most importantly, years of accrued expertise. Let’s delve into the key components that go into the creation of each transfer you order.
-
Industrial DTF Printer & Oven
These printers are specifically designed to transfer your unique artwork onto film with extraordinary accuracy. Paired with our high-efficiency dryers, they ensure the printed designs are perfectly set and ready for the next stage of the process.
-
Warm/Hot/Cold Peel Film
We utilize a hot peel. These films are selected carefully to ensure that your design is transferred onto the garment seamlessly, without compromising the vividness or the detail of your artwork.
-
Premium Matte Inks
Quality of the ink used plays a crucial role in bringing your designs to life. We utilize premium matte inks that offer exceptional color fidelity and longevity. These inks ensure your design remains vibrant and intact, even after numerous washes.
-
TPU (Thermoplastic Polyurethane) Powder
It is specifically designed to coat the printed adhesive and aids in binding your design to the garment during the heat transfer process. This ensures the durability of the design and allows it to withstand everyday wear and tear.
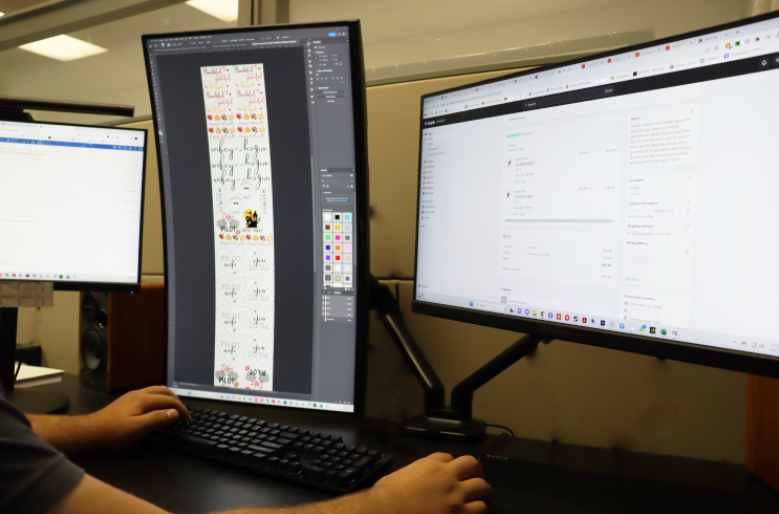
1. Prepress Quality Assurance
Prior to the initiation of the printing process, our dedicated team of specialists meticulously scrutinizes your artwork. The purpose of this review is to ensure that your design is optimized for our printing process. Once your artwork is deemed perfect, it is forwarded to our sophisticated, in-house prepress RIP (Raster Image Processor) software for the actual printing process.
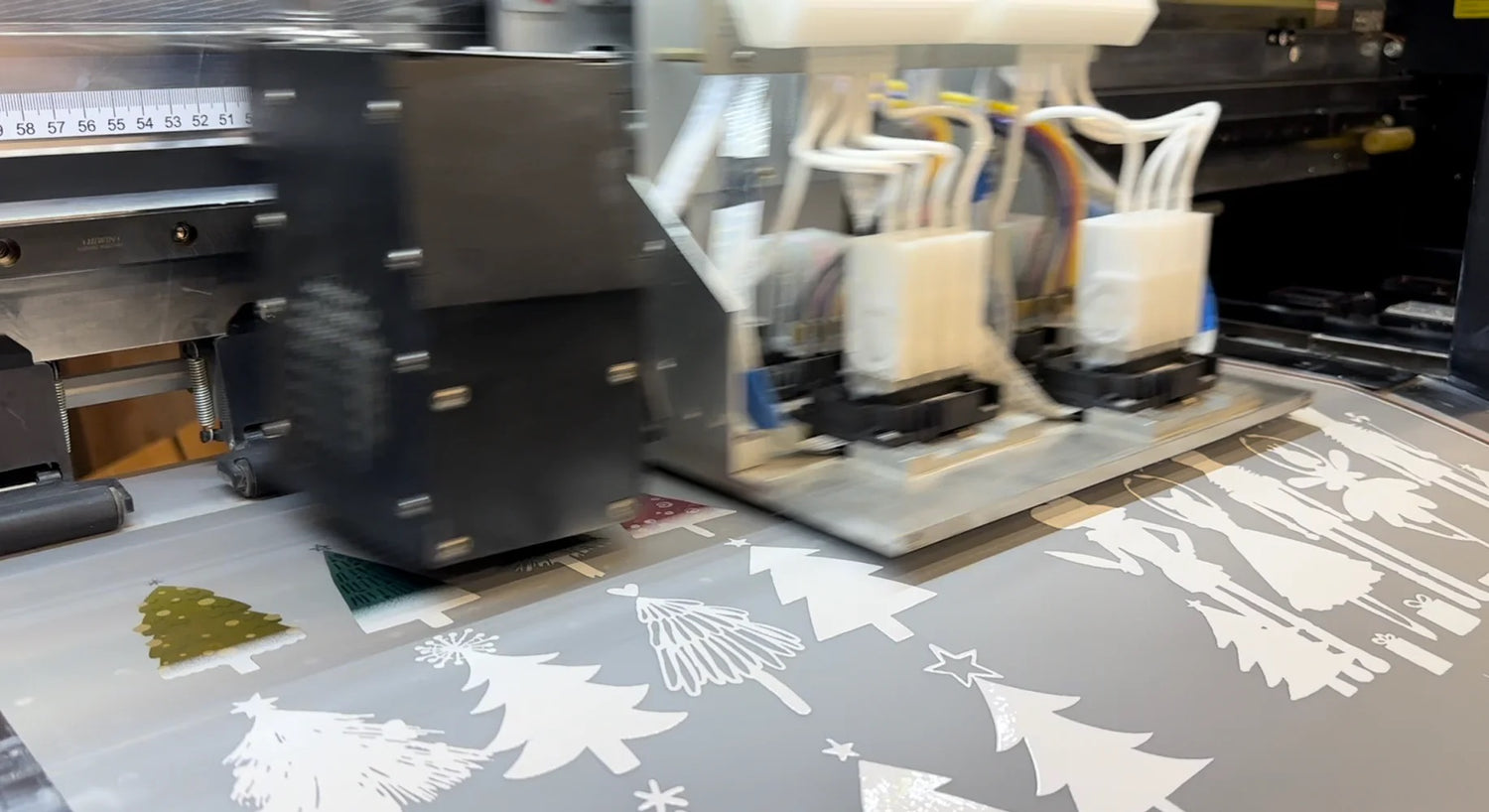
2. Precision Printing
Our state-of-the-art, industry-leading printers, equipped with quad head 3200 dpi print heads, take over from here. As your artwork is being precisely replicated, an underlayer of white is applied along with a heat-activated adhesive. This dual action guarantees excellent color representation and ensures optimal adhesion to the garment material.
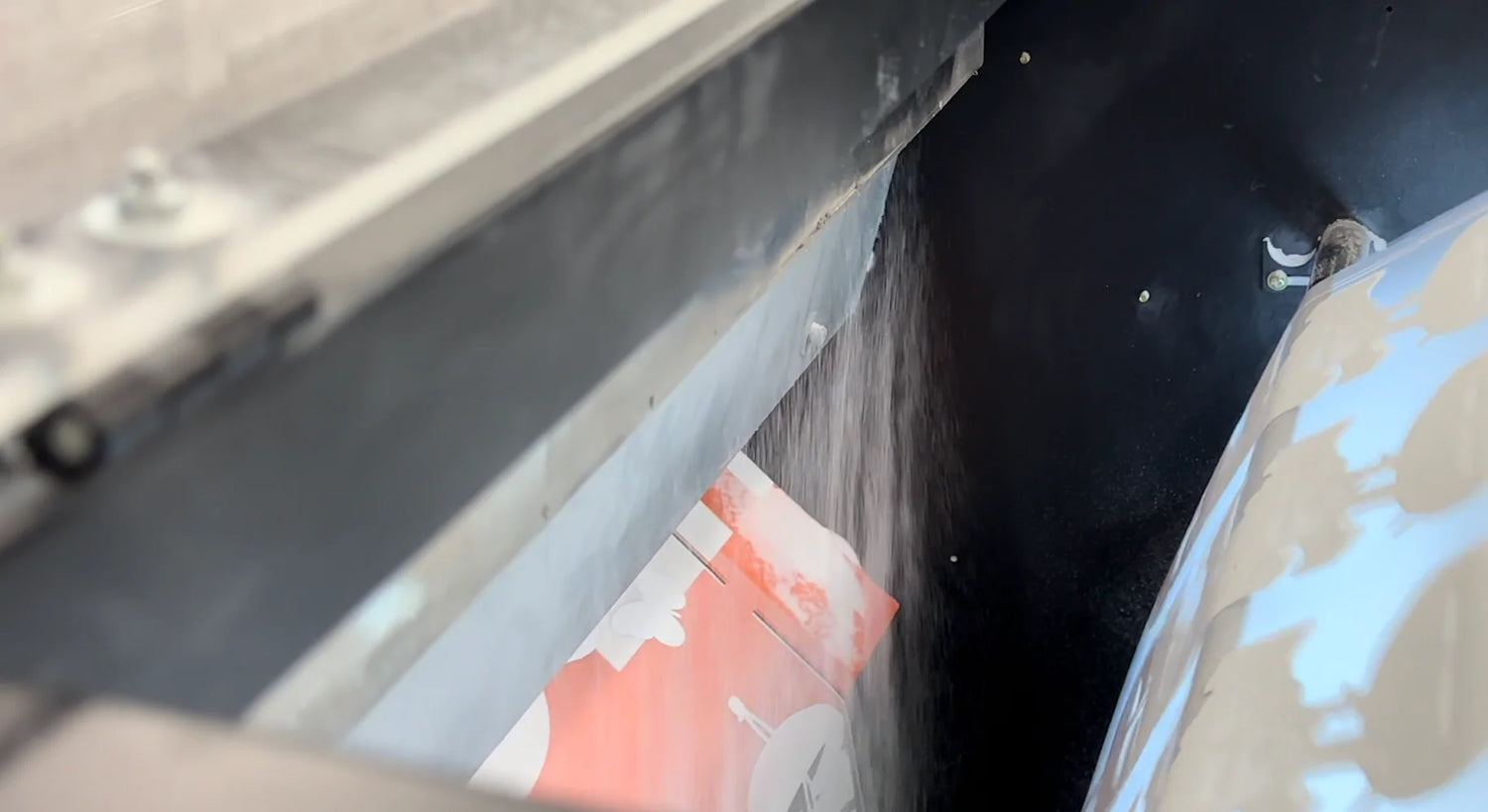
3. Powder Application
Subsequent to the printing stage, your design is carefully passed under a finely dispersed cloud of DTF (Direct To Film) specific thermoplastic polyurethane (TPU) powder. This fine powder adheres to the printed adhesive layer, setting the stage for the curing process.
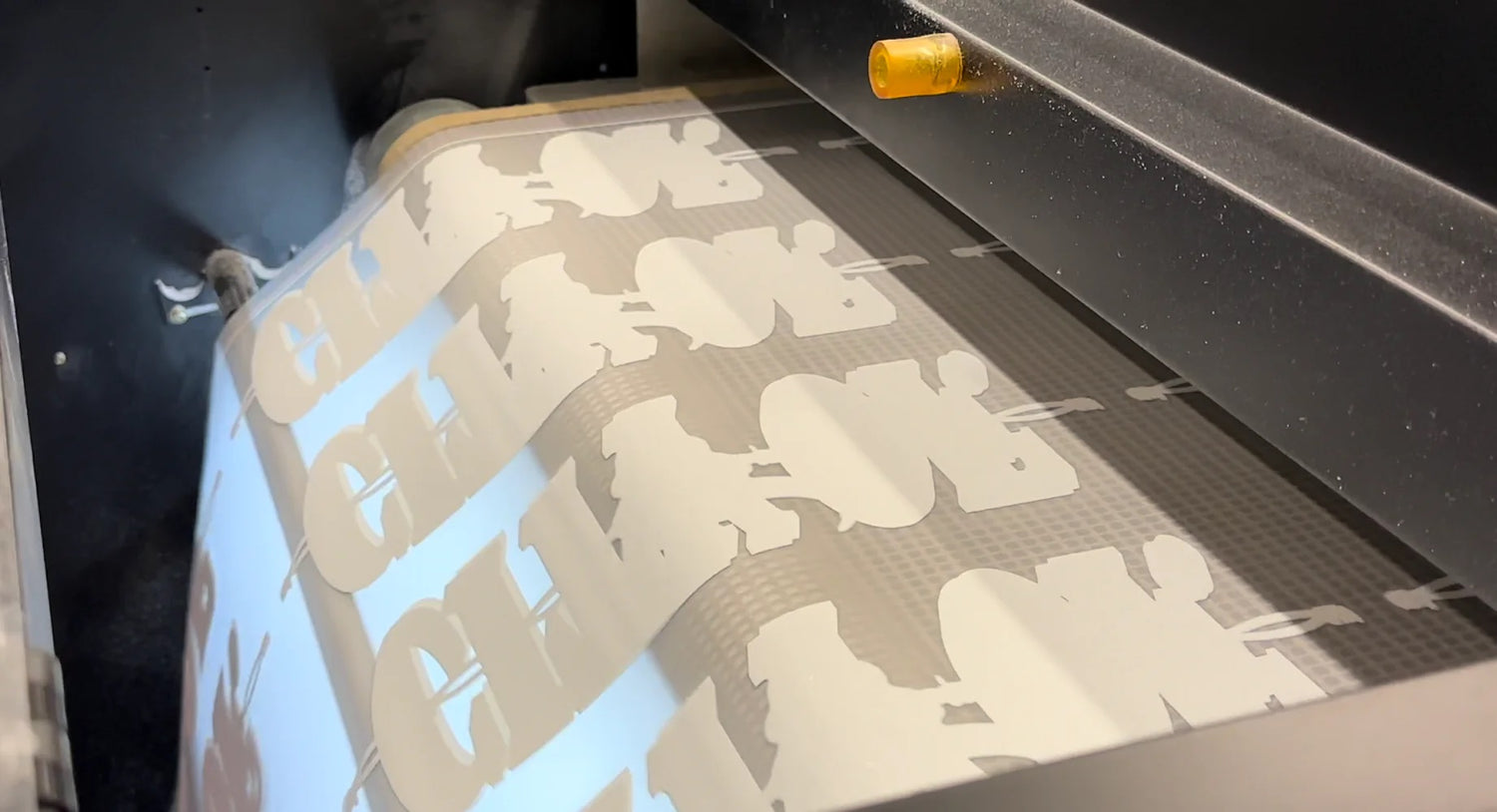
4. Exact Curing
In this stage, the printed design and adhering powder are subject to a controlled heating process, set to an exact temperature. This meticulous process serves to bind the powder and print, thereby maximizing the durability and longevity of your transfer, ensuring it can withstand washes without compromising the integrity of your design.
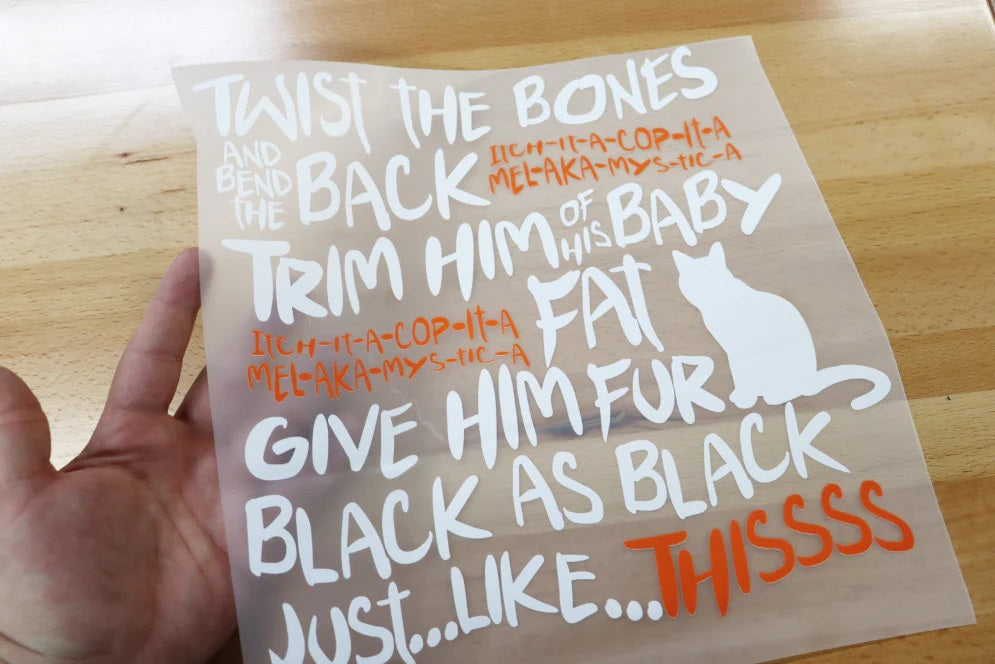
5. Final Inspection and Delivery
Following the curing process, each transfer undergoes a final, thorough inspection to ensure it meets our high-quality standards. Once the transfer passes this rigorous quality check, it is ready to be securely packaged and dispatched directly to your doorstep, primed for you to create your unique garment masterpiece.
We take immense pride in our transparent and meticulous process, ensuring you receive a product of the highest quality. Our team is always available to answer any queries you may have. Together, let’s make your artistic vision a tangible reality.